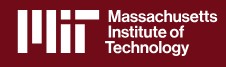
Microfabrication: Designed and created small bio
compatible parts using advanced poly jet and resin
printers. Examples include Teflon tubing with laser cut
holes with a diameter of 300 microns. Refined the
design in many iterations to get the settings optimized
for the laser, making sure the holes were clean and
that the 3D printed parts would assemble perfectly.
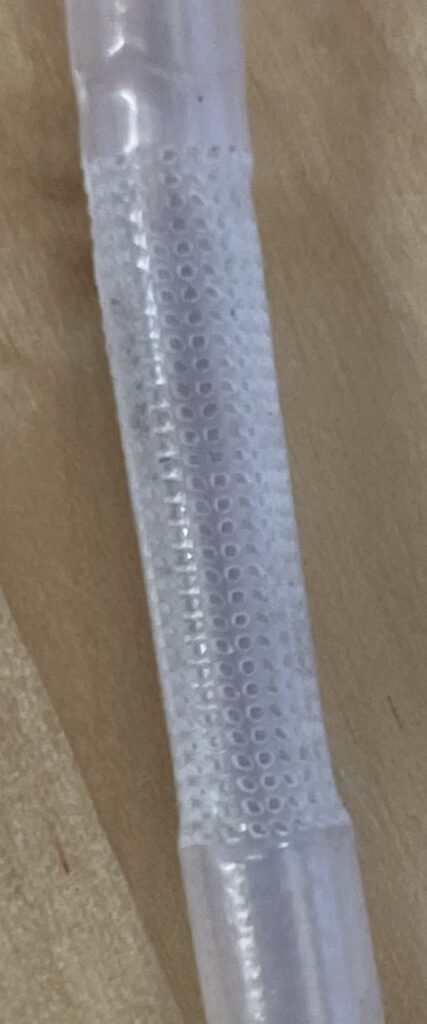
Injection molding projects: Multiple iteration and
testing with the Xplore Injection molder to fit optimal
settings for specified parts.
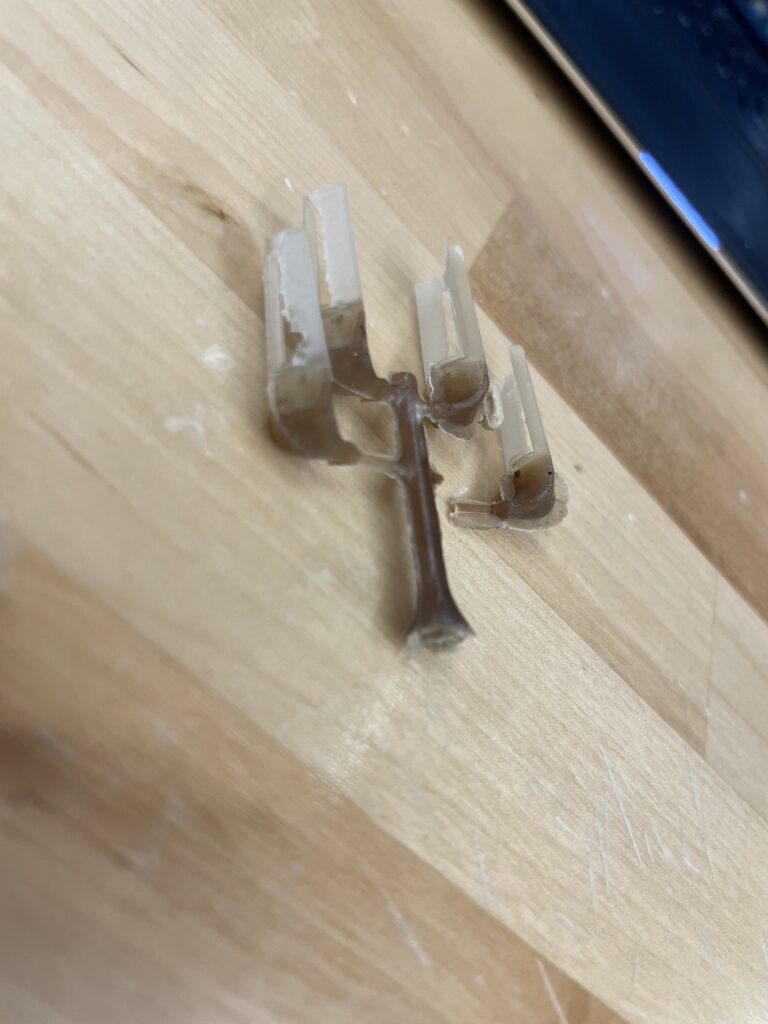
Equipment fume guard: While
using the micro-compounder I
noticed that fumes were not being
correctly funnel into the hood. I
manufactured a guide using
polycarbonate and 3D printed parts
to better direct airflow.
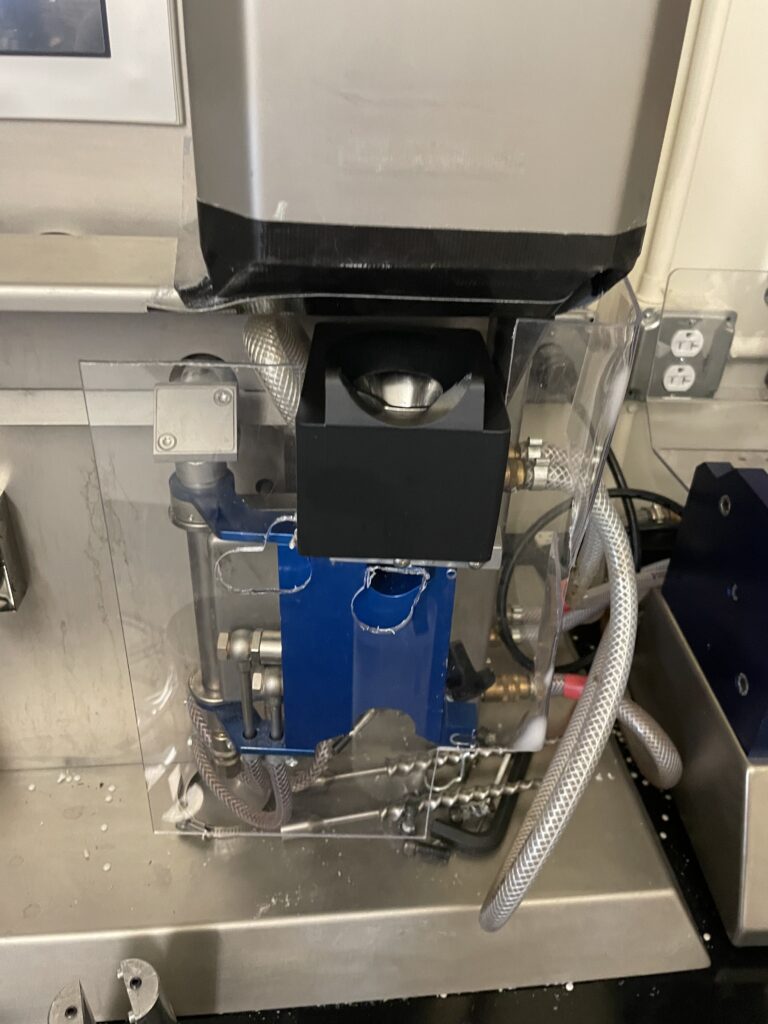
Microfabrication: Designed and created small bio
compatible parts using advanced poly jet and resin
printers. Examples include Teflon tubing with laser cut
holes with a diameter of 300 microns. Refined the
design in many iterations to get the settings optimized
for the laser, making sure the holes were clean and
that the 3D printed parts would assemble perfectly.
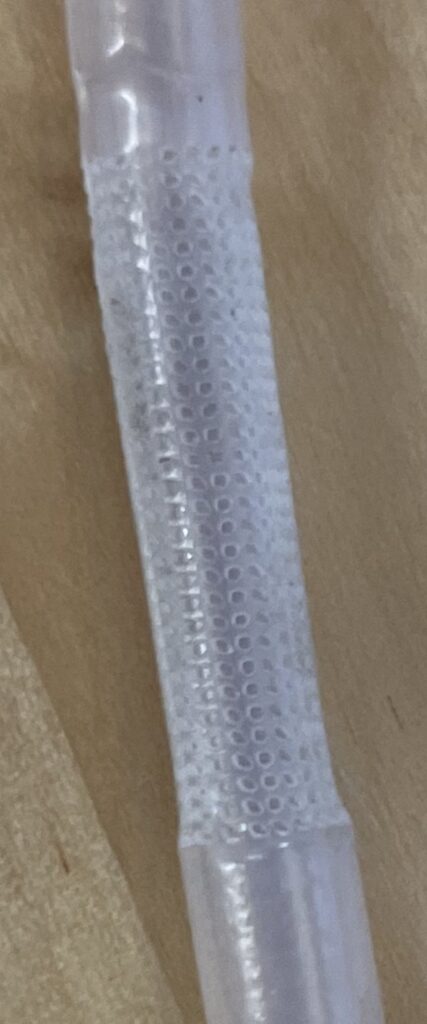
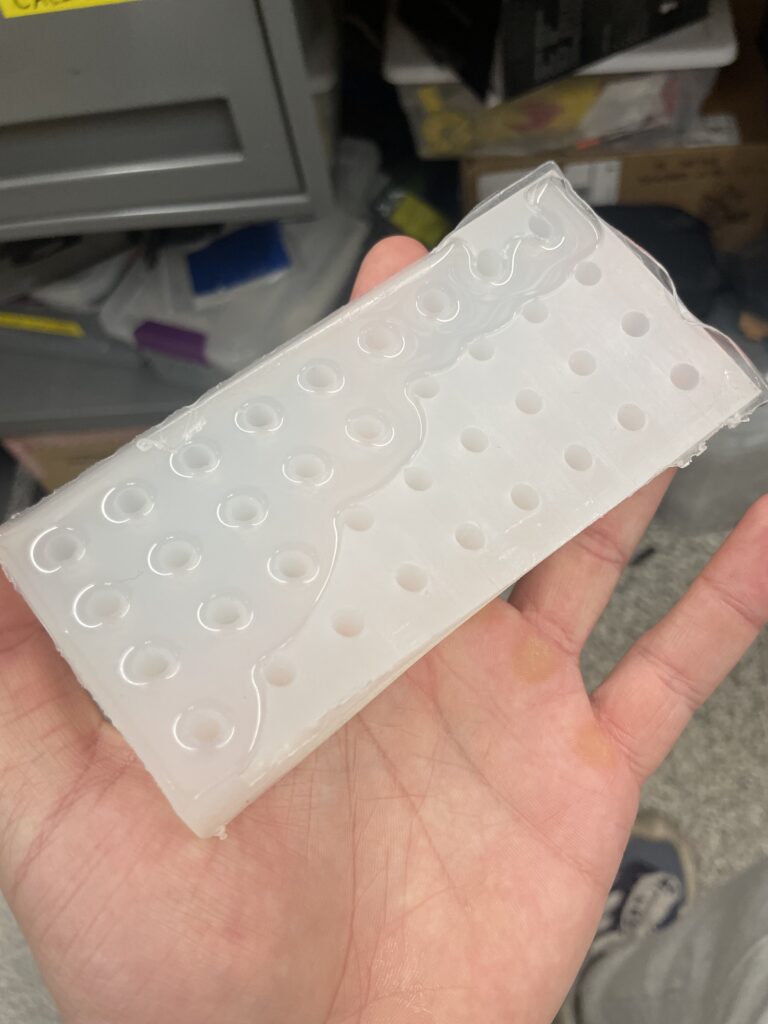
Molds: Designed and manufactured flexible silicon
molds. Iterated through various designs so that the
PDMS cast devices were consentient and efficient to
produce.
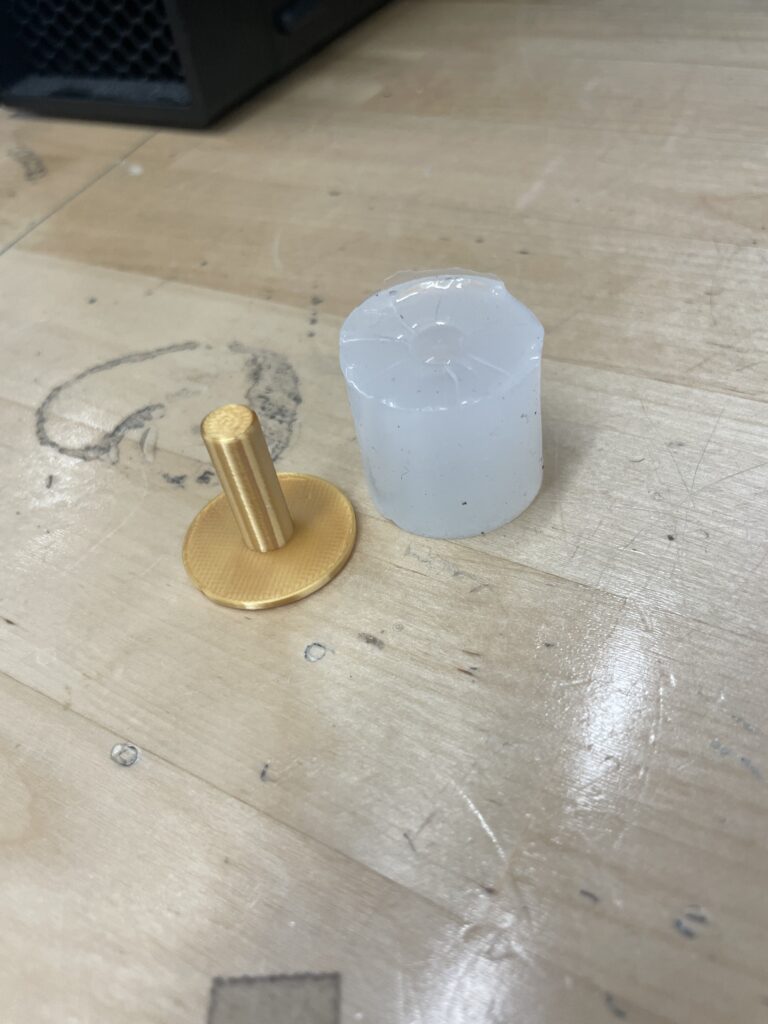
Magnet Inserter: Designed and manufactured a device that
improved the process for inserting magnets into a testing
device.
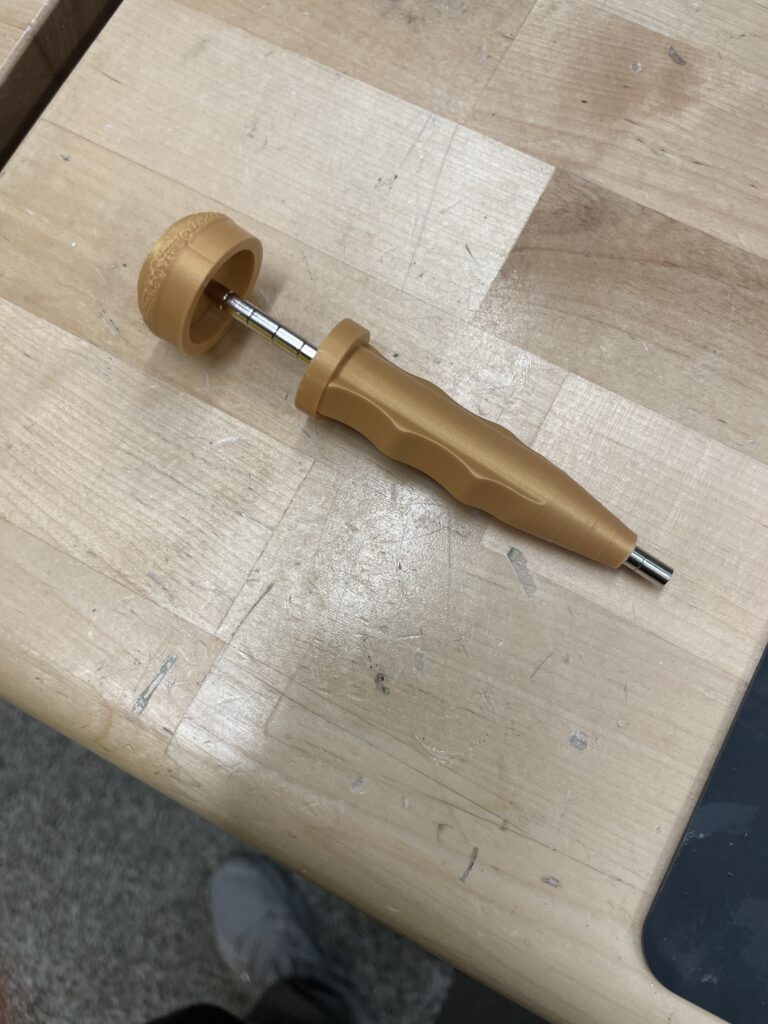